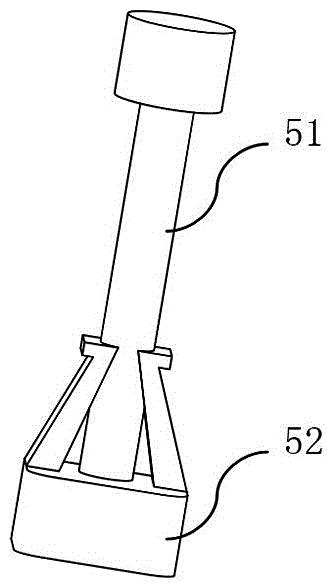
本发明涉及一种半导体器件互联装置及其方法,尤其是涉及一种实现功率半导体模块功率互联的装置及其方法。
背景技术:一个功率半导体模块半成品的组成由以下几个部分组成:母排、侧框和基板。为完成该功率半导体模块半成品,首先需要进行真空焊接工艺,完成功率半导体模块基板组件,在该真空焊接工艺中,可以同时实现母排的焊接。然后在功率半导体模块基板组件上安装侧框,最后在功率模块基板组件上进行PCB板的组装。功率模块实现功率互联,主要包括功率端的互联和辅助端的互联。在功率端互联方法上,国内、国外所有同类行业都是使用铜母排实现的,而在辅助端的互联方法上目前主要有三种。第一种辅助端互联的方法是使用导线连接:即使用手工焊接的方式,将作为辅助端引线用的导线两端分别焊接在功率模块电极上和辅助端母排上。这种方法由于需要对导线两端都进行手工焊接,实现效率比较低,手工操作可靠性较低,返修困难,不能适应大规模生产的要求。第二种辅助端互联的方法是使用引线键合的方式:使用超声引线键合技术,将键合铜带或铝带作为辅助端引线,实现功率模块电极和辅助端母排的连接。这种工艺方法可实现性强,效率也很高,但是实现成本较高,且超声引线键合点的强度相比焊接点要低,键合后即不可返修,所以比较适合于小功率的功率模块。第三种辅助端互联的方法是使用PCB板连接的方式:即使用PCB板作为辅助端引线和辅助端母排间的过渡,实现功率模块电极和辅助端母排的焊接。目前这种工艺仍然需要使用手工焊实现辅助端引线和辅助端母排与PCB板的焊接,但是相比较第一种方法效率更高,且相比较第二种方法得到的互联焊点也更可靠,是国内、国外大部分高压大功率模块制造厂家实现功率互所联采用的方法,但是如何能够更大程度上实现设备生产代替手工操作,一直是所有厂家研究的课题。现有的三种功率模块辅助端互联的方法中,第一种辅助端互联的方法由于需要导线两端都进行手工焊接,实现效率比较低,手工操作可靠性较低,返修困难,不能适应大规模生产的要求。第二种辅助端互联的方法工艺方法可实现性强,效率也很高,但是实现成本较高,且超声引线键合点的强度相比焊接点要低,键合后即不可返修,所以比较适合于小功率的功率模块。第三种辅助端互联的方法是使用PCB板,目前这种工艺仍然需要使用手工焊实现辅助端引线和辅助端母排与PCB板的焊接,但是相比较第一种方法效率更高,且相比较第二种方法得到的互联焊点也更可靠,是国内、国外大部分高压大功率模块制造厂家实现功率互所联采用的方法,但是如何能够更大程度上实现设备生产代替手工操作,一直是所有厂家研究的课题。
技术实现要素:有鉴于此,本发明的目的在于提供一种半导体模块功率互联装置及其方法,解决了现有技术存在的需要大量手工操作、效率低下、质量问题发生率高的问题。为了实现上述发明目的,本发明具体提供了一种半导体模块功率互联装置的技术实现方案,一种半导体模块功率互联装置,包括:母排、侧框、基板、印制电路板、辅助端引线组件和衬板组件。所述基板的边缘处设置有所述侧框,所述母排和所述衬板组件均设置在所述基板上,所述辅助端引线组件的一端与位于所述基板上的功率模块电极相连,所述辅助端引线组件的另一端与所述印制电路板相连,所述基板与所述印制电路板之间通过所述辅助端引线组件可活动的连接。优选的,所述印制电路板上进一步设置有辅助端母排。优选的,所述辅助端引线组件进一步包括第一组件和第二组件。所述辅助端引线组件的第一组件和第二组件之间通过契合或插接或卡钩方式连接。优选的,所述第一组件一端为第一焊接端,另一端为插头,所述第一焊接端焊接在所述印制电路板上。所述第二组件一端为插口,另一端为第二焊接端,所述第二焊接端焊接在所述功率模块电极上。所述插头和所述插口结合后形成可逆性契合结构。优选的,所所述第一组件采用台阶式结构,直径相对较大的一端为所述第一焊接端,直径相对较小的一端为所述插头。优选的,所述第二组件的插口包括两个用于夹持所述第一组件的插头的夹持部件,两个夹持部件之间形成具有两个缺口的半封闭圆形契合插口结构。优选的,所述半导体模块功率互联装置实现半导体模块之间的功率互联,所述母排分别与所述半导体模块的发射极和集电极相连。优选的,所述辅助端母排分别与所述半导体模块的发射极控制端、门极控制端和集电极控制端相连。本发明还另外具体提供了一种半导体模块功率互联方法的技术实现方案,一种半导体模块功率互联方法,包括以下步骤:S10:进行母排、基板、辅助端引线组件的第二组件和衬板组件的安装和焊接,将所述母排和所述衬板组件安装在所述基板上,将辅助端引线组件的第二组件一端焊接在所述基板的功率模块电极上;S20:进行辅助端引线组件的第一组件、辅助端母排和印制电路板之间的安装和焊接,将辅助端引线组件的第一组件的一端焊接在印制电路板上,在所述印制电路板上安装辅助端母排,形成待安装的印制电路板;S30:在步骤S10的基础上,在所述基板的边缘处加装侧框,完成中间工艺,形成待安装印制电路板的功率模块板;S40:将步骤S20中形成的待安装的印制电路板与步骤S30中形成的待安装印制电路板的功率模块板通过辅助端引线组件的第二组件和第一组件通过契合或插接或卡钩方式进行连接,形成安装印制电路板的功率模块板,进行后续工序处理。优选的,所述辅助端引线组件的第一组件和第二组件之间通过可逆性契合方式连接。优选的,在所述步骤S20与步骤S40之间进一步包括所述印制电路板清洗的工序。优选的,所述辅助端引线组件的第二组件通过真空回流焊焊接在所述功率模块电极上。优选的,所述辅助端母排和辅助端引线组件的第一组件通过波峰焊焊接在所述印制电路板上。通过实施上述本发明提供的一种半导体模块功率互联装置及其方法的技术方案,具有如下技术效果:(1)本发明半导体模块功率互联方法的工艺流程得到了大幅简化,操作流程步骤明显减少,工艺更加简单高效;(2)本发明提高了效率和质量,由于辅助端引线组件和印制电路板之间的焊接是在没有安装到功率模块上之前进行的,那么就为设备自动化实现提供了可能性,可以完全省去手工焊接的操作,所有焊接工艺使用设备自动化实现,在提高效率的同时,避免了人为因素导致的操作失误,提高了产品质量;(3)本发明返修容易,辅助端引线组件的第一组件和第二组件之间通过契合或插接或卡钩方式连接,可以随时取下或重新组装,使返修变得非常的方便。附图说明为了更清楚地说明本发明实施例或现有技术中的技术方案,下面将对实施例或现有技术描述中所需要使用的附图作简单地介绍,显而易见地,下面描述中的附图仅仅是本发明的一些实施例,对于本领域普通技术人员来讲,在不付出创造性劳动的前提下,还可以根据这些附图获得其他的附图。图1是本发明半导体模块功率互联装置一种具体实施方式的结构示意图。图2是本发明半导体模块功率互联装置一种具体实施方式辅助端引线组件的结构示意图。图3是本发明半导体模块功率互联装置一种具体实施方式辅助端引线组件的第一组件的结构示意图。图4是本发明半导体模块功率互联装置一种具体实施方式辅助端引线组件的第二组件的结构示意图。图5是本发明半导体模块功率互联方法一种具体实施方式将第二组件焊接到功率模块电极上的示意图。图6是本发明半导体模块功率互联方法一种具体实施方式将第一组件与印制电路板进行焊接的示意图。图7是本发明半导体模块功率互联方法一种具体实施方式中待安装印制电路板的功率模块的示意图。图8本发明半导体模块功率互联方法一种具体实施方式中完成组装的半导体模块功率互联装置的结构示意图。图9是本发明半导体模块功率互联方法一种具体实施方式的操作流程图。图中:1-母排,2-侧框,3-基板,4-印制电路板,5-辅助端引线组件,51-第一组件,511-第一焊接端,512-插头,52-第二组件,521-插口,522-第二焊接端,6-功率模块电极,7-衬板组件,8-辅助端母排。具体实施方式为了引用和清楚起见,将下文中使用的技术名词、简写或缩写记载如下:IGBT:InsulatedGateBipolarTransistor,绝缘栅门极双极型晶体管的简称;PCB:PrintedCircuitBoard,印制电路板的简称。为使本发明实施例的目的、技术方案和优点更加清楚,下面将结合本发明实施例中的附图,对本发明实施例中的技术方案进行清楚、完整地描述,显然,所描述的实施例仅仅是本发明的一部分实施例,而不是全部的实施例。基于本发明中的实施例,本领域普通技术人员在没有作出创造性劳动前提下所获得的所有其他实施例,都属于本发明保护的范围。如附图1至附图9所示,给出了本发明一种半导体模块功率互联装置及其方法的具体实施例,下面结合附图和具体实施例对本发明作进一步说明。如附图1和附图5所示的一种半导体模块功率互联装置的具体实施方式,包括:母排1、侧框2、基板3、印制电路板4、辅助端引线组件5和衬板组件7。基板3的边缘处设置有侧框2,母排1和衬板组件7均设置在基板3上。辅助端引线组件5的一端与位于基板3上的功率模块电极6相连,辅助端引线组件5的另一端与印制电路板4相连,基板3与印制电路板4之间通过辅助端引线组件5可活动的连接。在附图1中,省略了辅助端母排8。作为本发明一种典型的实施方式,如附图2所示的辅助端引线组件5进一步包括第一组件51和第二组件52。如附图3所示,第一组件51一端为第一焊接端511,另一端为插头512,第一焊接端511焊接在印制电路板4上。如附图4所示,第二组件52一端为插口521,另一端为第二焊接端522,第二焊接端522焊接在功率模块电极6上。插头512和插口521结合后形成可逆性契合结构,并采用过盈配合方式实现契合连接,从而实现导电连接功能。插头512和插口521之间还可以通过卡钩或插接方式连接。作为本发明一种典型的实施方式,第一组件51采用台阶式结构,直径相对较大的一端为第一焊接端511,直径相对较小的一端为插头512。印制电路板4上进一步设置有辅助端母排8。第二组件52的插口521进一步包括两个用于夹持第一组件51的插头512的夹持部件,两个夹持部件之间形成具有两个缺口的半封闭圆形契合插口结构。需要特别说明的是,虽然在实际应用中,第一组件51的插头512和第二组件52的插口521的截面均采用圆形,但是插头512和插口521的截面还可以采用包括圆形在内的正方形、矩形、椭圆形和任意多边形在内的任意形状。如附图8所示,半导体模块功率互联装置实现半导体模块之间的功率互联。半导体模块以一种典型的IGBT模块为例,半导体模块功率互联装置的母排1共包括三对主母排,为功率端口,与外部功率端接口相连接,每一对主母排分别为集电极母排和发射极母排,分别与半导体模块的集电极和发射极相连。每组发射极母排之间是相连的,每组集电极母排间是相互独立的。辅助端母排8包括三个控制极母排,分别是控制端集电极母排、控制端发射极母排和控制端门极母排,是控制端口,与外部的半导体模块控制电路或驱动电路相连接。辅助端母排8分别与半导体模块的发射极控制端、门极控制端和集电极控制端相连。其中,控制端发射极母排与所有发射极母排是相连的,控制端集电极母排与其中一组集电极母排是相连的。如附图9所示一种半导体模块功率互联方法的具体实施方式,包括以下步骤:S10:在特别设计的焊接工装辅助下,进行母排1、基板3、辅助端引线组件5的第二组件52和衬板组件7的安装、焊接,将辅助端引线组件5的第二组件52一端焊接在所述基板3的功率模块电极6上,如附图5所示;S20:进行辅助端引线组件5的第一组件51、辅助端母排8和印制电路板4之间的安装、焊接,将辅助端引线组件5的第一组件51的一端焊接在印制电路板4上,在印制电路板4上安装、焊接辅助端母排8,形成待安装的印制电路板4,如附图6所示;S30:在步骤S10的基础上,在基板3的边缘处加装侧框2,完成中间工艺,形成待安装印制电路板4的功率模块板,如附图7所示;S40:将步骤S20中形成的待安装的印制电路板4与步骤S30中形成的待安装印制电路板4的功率模块板通过辅助端引线组件5的第二组件52和第一组件51通过契合或插接或卡钩方式进行连接,形成安装印制电路板4的功率模块板,进行后续工序处理如附图8所示为完成了印制电路板组装的半导体模块功率互联装置。辅助端引线组件5的第一组件51和第二组件52之间通过可逆性契合方式连接。在步骤S20与步骤S40之间还进一步包括印制电路板4清洗的工序。辅助端引线组件5的第二组件52进一步通过真空回流焊焊接在功率模块电极6上。辅助端母排8和辅助端引线组件5的第一组件51进一步通过波峰焊焊接在印制电路板4上。本发明具体实施所描述的一种半导体模块功率互联装置及其方法,以最为简洁的工艺方法实现了功率模块的功率互联。其辅助端引线组件的结构设计,以一个独特的方法,将辅助端引线组件的两端相互独立进行焊接,操作流程步骤明显减少,工艺流程极大简化,使工艺更加简单高效。由于辅助端引线组件5和印制电路板4之间的焊接是在没有安装到功率模块上之前进行的,那么就为设备自动化实现提供了可能性,可以完全省去手工焊接的操作,所有焊接工艺使用设备自动化实现,在提高效率的同时,避免了人为因素导致的操作失误,提供了产品质量。同时,现有技术中不论是使用导线实现辅助端功率互联,或使用引线键合实现辅助端功率互联,还是传统的PCB板方式实现辅助端功率互联,其功率模块和辅助端引线、辅助端母排之间的连接都是固定死的,当功率模块需要返修时就会比较困难,而在本发明中,辅助端引线组件5的第一组件51和第二组件52之间是靠插口契合的,可以随时取下或重新组装,使返修变得非常的方便。本发明通过对功率模块,如高压IGBT模块的印制电路板结构进行优化设计和改变传统中实现互联的方式,可以更方便、高效的实现模块的衬板组件7、辅助端引线组件5、印制电路板4、辅助端母排8之间的互联,解决了传统技术中需要大量手工操作、效率低下、质量问题发生率高的问题。本说明书中各个实施例采用递进的方式描述,每个实施例重点说明的都是与其他实施例的不同之处,各个实施例之间相同相似部分互相参见即可。以上所述,仅是本发明的较佳实施例而已,并非对本发明作任何形式上的限制。虽然本发明已以较佳实施例揭露如上,然而并非用以限定本发明。任何熟悉本领域的技术人员,在不脱离本发明的精神实质和技术方案的情况下,都可利用上述揭示的方法和技术内容对本发明技术方案做出许多可能的变动和修饰,或修改为等同变化的等效实施例。因此,凡是未脱离本发明技术方案的内容,依据本发明的技术实质对以上实施例所做的任何简单修改、等同替换、等效变化及修饰,均仍属于本发明技术方案保护的范围内。