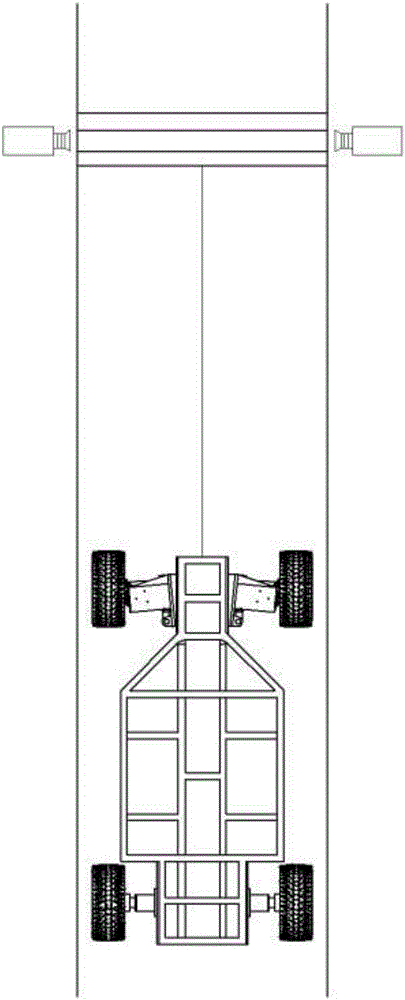
本发明涉及汽车零部件模拟试验领域,具体涉及一种用于车轮模拟实况冲击试验的车辆及系统。
背景技术:
:目前在进行车轮模拟冲击试验时,往往采用台架方法来进行径向冲击、13度冲击等试验,从而考察车轮在各种冲撞条件下的反应并判断车轮是否符合汽车生产商及使用者的要求。台架试验是对现实驾驶条件的模拟,其模拟结果可能无法完全反映实际驾驶过程中遇到各种不理想路面的真实反应。为了提供交通事故条件下的车辆质量,整车厂商往往使用真车冲撞墙面等试验来考察整车在交通事故下的表现。然而目前还没有针对车轮等零部件在非事故条件下的考验来进行试验的方法和装置。技术实现要素:为了在非事故条件下对车轮等零部件进行模拟实况冲击试验,本发明提供了一种用于车轮模拟实况冲击试验的车辆及系统。本领域的技术人员知道,在汽车的行驶过程中可能遭遇路面上的凸起物。该凸起物可能是泥土路面上的隆起部分、村道或乡镇道路上为农业浇灌而铺设的水管及护泥、小区或学校周边铺设的减速带或者道路上出现的其他隆起物或者障碍物。汽车行驶过程中也可能遭遇凹陷,凹陷可能是泥土路面、沥青路面和水泥路面上的凹陷部分,路面涂层型减速带等等。汽车当行驶通过以上的路面结构时,车胎将对车轮造成一定的作用力。该作用力随后通过轴和悬挂系统分散到车身。作为直接面对冲击的汽车零部件,车轮在这一行驶事件中可能遭受损伤。作为车轮生产企业,中信戴卡希望在更接近现实状态的条件下进行车轮性能检测。在本发明的一个方面,提供了一种用于车轮模拟实况冲击试验的车辆,所述的车辆由碰撞车辆总成(1)和测试的实车车轮及悬架系统(2)构成,其特征在于:所述的碰撞车辆总成(1)包括台车车体(101)、砝码及固定装置(102)、后轮及轮轴总成(103)和牵引挂钩适配机构(104);所述的台车车体(101)中部设置有砝码及固定装置(102),在台车车体(101)前部安装有测试的实车车轮及悬架系统(2),台车车体(101)后部安装后轮及轮轴总成(103),并且台车车体(101)底部固定有牵引挂钩适配机构(104)。在本发明优选的方面,所述的台车车体(101)由方管钢材焊接而成,并且其底部铺设有钢板。在本发明优选的方面,所述的砝码及固定装置(102)包括位于固定到台车车体(101)前部、中部和后部的砝码,并且固定到台车车体(101)前部、中部和后部的砝码分别为50~200千克、50~400千克和50~200千克。在本发明进一步优选的方面,所述的砝码及固定装置(102)中单块的砝码为直径400mm,厚度50mm的圆柱体,中间有直径60mm的通孔;单块的砝码通过固定杆固定到台车车体(101),固定杆为长度500mm,M48的螺纹杆;固定杆底端通过螺纹固定在台车底部车体上。在本发明优选的方面,所述的测试的实车车轮及悬架系统(2)包括测试车轮轮胎(201)、轮毂轴承(202)、转向节(203)、阻尼器及弹簧(204)、转向拉杆(205)、控制臂(206)和悬架固定背板(207);测试车轮轮胎(201)、轮毂轴承(202)、转向节(203)、阻尼器及弹簧(204)、转向拉杆(205)和控制臂(206)按照真车的装配方式进行装配;控制臂(206)和阻尼器及弹簧(204)分别固定到悬架固定背板(207);悬架固定背板(207)固定到台车车体(101)。在本发明进一步优选的方面,所述的轮毂轴承(202)、转向节(203)、阻尼器及弹簧(204)、转向拉杆(205)和控制臂(206)是待测车轮轮胎(201)真车装配配套的部件。在本发明的另一个方面,还提供了一种用于车轮模拟实况冲击试验的系统,所述的系统包括前文所述的用于车轮模拟实况冲击试验的车辆、路面(3)、高频照明设施(4)、标准障碍物块(5)、高速摄像机(6)、牵引电机及钢缆(7);牵引电机及钢缆(7)的牵引电机固定到路面(3)的第一端并且与钢缆的第一端固定,钢缆的另一端固定到车轮模拟实况冲击试验的车辆的牵引挂钩适配机构(104);前文所述的用于车轮模拟实况冲击试验的车辆位于路面(3)的第一端;标准障碍物块(5)固定到路面(3)的第二端;高速摄像机(6)安装到路面(3)侧面,标准障碍物块(5)上方;高频照明设施(4)安装到标准障碍物块(5)的上方。在本发明的另一个方面,还提供了使用前文所述的用于车轮模拟实况冲击试验的系统来进行车轮模拟实况冲击试验的方法,其包括步骤:(A)将待测车轮轮胎(201)所对应的真车的装配条件下的轮毂轴承(202)、转向节(203)、阻尼器及弹簧(204)、转向拉杆(205)和控制臂(206)组装到实车车轮及悬架系统(2),并且通过悬架固定背板(207)固定到台车车体(101);(B)按照待测车轮轮胎(201)所对应的真车的车重,在台车车体(101)前部、中部和后部固定砝码,构成砝码及固定装置(102);(C)对安装好的用于车轮模拟实况冲击试验的车辆进行前轮定位校正,以保证其在牵引电机及钢缆(7)的驱动下沿着直线运动;(D)将安装好的用于车轮模拟实况冲击试验的车辆移动到路面(3)的第一端,并且固定到牵引电机及钢缆(7);(E)在路面(3)设置标准障碍物块(5);(F)开启高频照明设施(4)和高速摄像机(6);(G)通过牵引电机及钢缆(7)牵引用于车轮模拟实况冲击试验的车辆;(H)车轮通过障碍物块时,高速摄像机录像,然后减速停车;(I)检查车轮变形情况。在本发明一个具体的方面,在步骤(F)中,牵引使得用于车轮模拟实况冲击试验的车辆速度为40-80km/h。在本发明一个具体的方面,牵引使得用于车轮模拟实况冲击试验的车辆速度为64kM/h,所使用的轮胎为205/55R16型号轮胎,轮胎的胎压为200kPa,满载前轴重为900kg,后轴重820kg。本发明的用于车轮模拟实况冲击试验的车辆及系统的优点在于,通过使用通配型的碰撞台车,使得可以使用一套设备来满足多种车轮的测试需求,从而避免针对每一款车轮使用相应的真车来进行试验。这使得试验成本大为降低,同时还确保了试验状态接近真车状态,能较好地模拟真车遇见障碍物的过程中的表现。附图说明以下,结合附图来详细说明本发明的实施方案,其中:图1是本发明的实施例1的用于车轮模拟实况冲击试验的系统的组成示意图;图2是本发明的实施例1的用于车轮模拟实况冲击试验的系统的俯视图;图3是本发明的实施例1的碰撞台车的侧视图;图4是本发明的实施例1的碰撞台车的后视图;图5是本发明的实施例1的碰撞台车的俯视图;图6是本发明的实施例1的碰撞台车的立体图;图7是本发明的实施例1的碰撞台车的立体组装状态图;图8是本发明的实施例1的测试的实车车轮及悬架系统(2)的结构示意图;图9是本发明的实施例1的测试的实车车轮及悬架系统(2)的装配示意图;图10是本发明的实施例2的凸起障碍物的结构示意图;图11是本发明的实施例2的凹陷障碍物的结构示意图;图中:1-碰撞车辆总成、2-测试的实车车轮及悬架系统、3-路面、4-高频照明设施、5-标准障碍物块、6-高速摄像机、7-牵引电机及钢缆、101-台车车体、102-砝码及固定装置、103-后轮及轮轴总成、104-牵引挂钩适配机构、201-测试车轮轮胎、202-轮毂轴承、203-转向节、204-阻尼器及弹簧、205-转向拉杆、206-控制臂、207-悬架固定背板、1001-凸起障碍物块、1002-三轴力传感器、1003-传感器底座、1005-凸起障碍物块的槽沟、1101-凹陷障碍物块、1102-三轴力传感器、1103-传感器底座和1105-凹陷障碍物块的槽沟。具体实施方式实施例1:用于车轮模拟实况冲击试验的车辆和系统在本实施例中,图1中各系统单元组成了车轮和悬架系统的实况冲击试验的设备,主要由碰撞车辆总成(1)、测试的实车车轮及悬架系统(2)、标准50m~200m跑道(3)、高频照明设施(4)、标准障碍物块(5)、高速摄像机(6)、牵引电机及钢缆(7)组成。碰撞台车、车轮及悬架系统的总成示意图由台车车体(101)、砝码及固定装置(102)、后轮及轮轴总成(103)、牵引挂钩适配机构(104)和车轮悬架总成(2)构成。车体(101)由方管钢材焊接而成,底部铺设有钢板,钢板上布置了6个用于固定砝码固定杆的孔。实际测试时,通过调整每一个砝码固定杆上的砝码数量,实现对整车前轮负重和后轮负重,以及整车重心位置的精确控制调整。在车体的底部,设有牵引挂钩适配机构(104)。砝码及固定装置(102)由砝码块、固定杆、锁定螺母三部分组成。其中单块的砝码为直径400mm,厚度50mm的圆柱体,中间有直径60mm的通孔。固定杆长度为500mm,M48的螺纹杆,底端通过螺纹固定在台车底部车体上。锁定螺母为自制的M48外六方螺母。后轮及轮轴总成(103)由后车轮、轮轴总结两部分组成,通过螺栓紧固在车体上。车轮和轮胎可任意选用(因测试主要是评估前轮,而后轮只起协助行驶的作用),轮轴为自制。车轮和悬架系统总成。由测试车轮轮胎(201)、轮毂轴承(202)、转向节(203)、阻尼器及弹簧(204)、转向拉杆(205)、控制臂(206)、悬架固定背板(207)组成。轮毂轴承(202)、转向节(203)、阻尼器及弹簧(204)、转向拉杆(205)、控制臂(206)均为2015款大众高尔夫1.4T车的原车配件,购自本地汽配城。具体的连接方式为:转向节(203)与阻尼器及弹簧(204)、转向拉杆(205)、控制臂(206)、悬架固定背板(207)按实际装车的装配关系组成悬架系统,将轮毂轴承安装在转向节上,安装方式等同与在原车上的装配关系。将测试车轮和装车用原装轮胎组织到一起,充气至胎压200kPa后,通过螺栓固定在轮毂轴承上,等同于车辆上的装配。实施例2:车轮模拟实况冲击试验本实施例按照以下的步骤来进行:1.确定试验需求。对2015款大众高尔夫1.4T车型左前位置车轮进行64km/h下模拟实况冲击路面凸起障碍物标准块试验。2.确定试验参数。冲击速度=64kM/h;轮胎=205/55R16;胎压=200kPa;满载前轴重为900kg,后轴重820kg。3.准备悬架总成。在市场上(汽配城)采购高尔夫车型的轮毂轴承、转向节、阻尼器及螺旋弹簧、转向拉杆、控制臂等悬架零部件。按原车装配参数设计制成悬架固定背板。将其以等效于原车悬架装配的方式组成试验台车用悬架系统。4.悬架与台车车体装配。用螺钉将组建好的悬架系统通过背板上的螺孔固定在台车车体上。5.取全新的测试车轮样品,装胎,充气并做动平衡。用等同于车辆上的安装方式将车轮轮胎总成安装到悬架轮毂轴承上。6.对安装好前轮和悬架的试验台车总成进行前轮定位校正,以保障其能按直线行驶。7.将台车移动至发车区,连接牵引挂钩。8.设定好灯光和摄像系统。保证车辆在碰撞的时刻他们能正常工作。9.牵引系统通过挂钩牵引车辆加速至64km/h。10.车轮通过障碍物块时,高速摄像机录像,然后减速停车。11.检查车轮变形情况。其中,固定障碍物包括凹陷障碍物或者凸起障碍物。凹陷障碍物由凹陷障碍物块(1101)、三轴力传感器(1102)、传感器底座(1103)和凹陷障碍物块的槽沟(1105)构成,其特征在于:所述的凹陷障碍物块的槽沟(1105)位于路面(1104)上;传感器底座(1103)安放在凹陷障碍物块的槽沟(1105)的底部;三轴力传感器(1102)的一端安装在传感器底座(1103)的上表面,另一端安装到凹陷障碍物块(1101)的下表面;所述的凹陷障碍物块(1101)沿凹陷障碍物块的槽沟(1105)的长度方向的横截面具有梯形的凹陷;并且,所述的凹陷障碍物块(1101)设置为当安装完毕后,凹陷的梯形的底边和路面(1104)平齐。所述的凹陷障碍物块(1101)沿凹陷障碍物块的槽沟(1105)的长度方向的横截面的等腰梯形部分的长底边长度为1400mm,短底边长度为100mm,梯形的高度为120mm,凹陷障碍物块(1101)的顶部宽度为1600mm。在道路上设置的凹坑中,将障碍物、三轴力传感器、传感器底板按上述连接方式固定,用一定速度的车辆去通过障碍物,设置在障碍物底下的四个三轴力学传感器连接高速数字采集仪,能得到冲击过程中的力学曲线,通过对四个传感器进行数学耦合,计算出障碍物的受的合力,即为冲击力。凸起障碍物由凸起障碍物块(1001)、三轴力传感器(1002)、传感器底座(1003)和凸起障碍物块的槽沟(1005)构成,其特征在于:所述的凸起障碍物块的槽沟(1005)位于路面(1004)上;传感器底座(1003)安放在凸起障碍物块的槽沟(1005)的底部;三轴力传感器(2)的一端安装在传感器底座(1003)的上表面,另一端安装到凸起障碍物块(1001)的下表面;所述的凸起障碍物块(1001)沿凸起障碍物块的槽沟(1005)的长度方向的横截面在上部为梯形;并且,所述的凸起障碍物块(1001)设置为当安装完毕后,梯形的底边和路面平齐。所述的凸起障碍物块(1001)沿凸起障碍物块的槽沟(1005)的长度方向的横截面的等腰梯形部分的长底边长度为430mm,短底边长度为100mm,梯形的高度为80mm。所述的凸起障碍物块(1001)沿凸起障碍物块的槽沟(1005)的长度方向的横截面下部为矩形,矩形的尺寸为430×70mm。在道路上设置的凹坑中,将障碍物、三轴力传感器、传感器底板按上述连接方式固定。用一定速度的车辆去通过障碍物,设置在障碍物底下的四个三轴力传感器连接高速数字采集仪,能得到冲击过程中的力学曲线,通过对四个传感器进行数学耦合,计算出障碍物的受的合力。对比例1:车轮的台架试验选择与实施例2中同款车轮一只,装胎205/55R16充气,按QC/T991-2015行业标准规定的试验方法,对车轮进行90°冲击试验,能量选择为E2级。测得车轮受最大冲击力是=56.1KN,轮缘变形量是8.63mm。对比例2:车轮的真车试验对2015款大众高尔夫1.4T车型实车的左前位置车轮进行80km/h下模拟实况冲击路面凸起障碍物标准块试验。为了保证安全提前在车身内部安装防翻滚架,试车驾驶员穿安全服佩戴头盔。测试路面上放置凸起标准障碍物块。车辆前轴重调整至900kg,后轴重820kg。驾驶车辆在64km/h速度下,使左前轮通过标准障碍物块,测得冲击力为37.7kN。冲击完成后卸下车轮,发现车轮轮辋变形量为1.1mm。实施例3:车轮变形试验结果实施例2和对比例1~2选择了同样的标准障碍物块具有可比性。将实施例2、对比例1~2中测得的试验数据放入表1进行比较,发现模拟实车冲击系统(实施例2)较台架试验(对比例1)更加接近实际车辆行驶中撞击结果(对比例2)。表1实施例2与对比例1~2的试验结果试验组测得冲击力(KN)测得变形量(mm)实施例236.01.5对比例156.18.63对比例237.71.1从试验结果可以看出,台架试验与真车试验存在着很大的差异,主要是因为台架试验时无法把车辆悬架安装上,冲击力只能全部由车轮来吸收。而实施例2用等效车辆装配的方式把车轮及悬架安装在一台模拟车辆上,进行冲击试验的效果已非常的接近对比例2的实际车辆冲击情况。当前第1页1 2 3