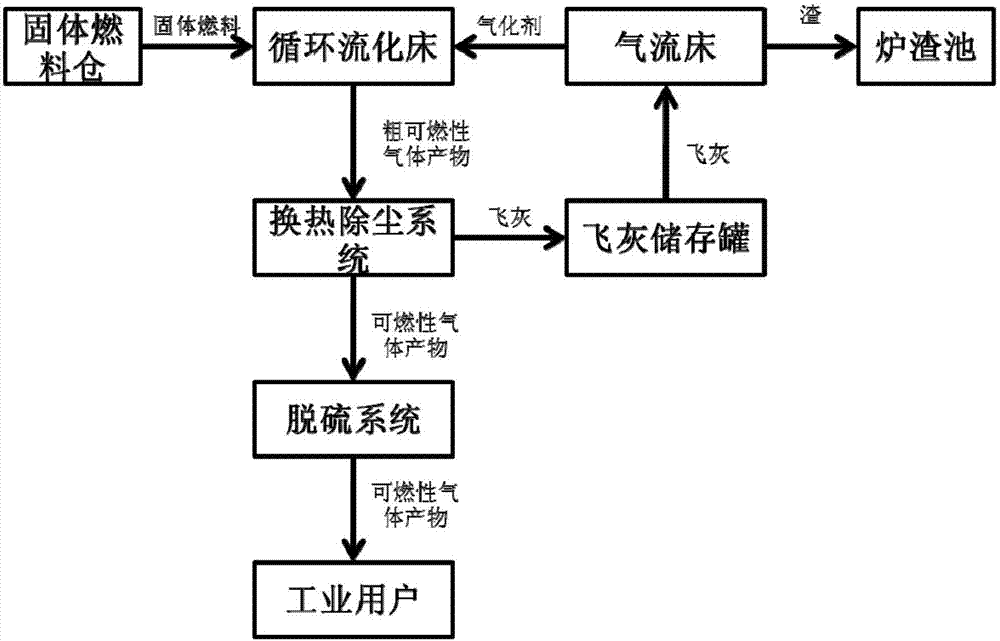
本发明涉及节能环保
技术领域:
,尤其涉及一种气流床与循环流化床组合循环气化系统及其两段式气化方法。
背景技术:
:气化技术是指将固体燃料与气化剂在在一定温度和压力下发生氧化还原反应,从而得到可燃性气体产物的过程目前工业气化技术根据燃料和气化剂的接触方式主要分为固定床术、流化床和气流床气化技术。常用的固定床气化技术具有结构简单、操作便利、运行方便灵活等优点,但普遍存在机械化、自动化程度较低,处理量小、碳转化效率低、生产的燃气杂质较多且难以处理,严重困扰该气化技术的进一步放大和清洁使用;流化床气化与固定床气化相比有以下优点:传热传质均匀,机械化、自动化程度高,易于放大等。但流化床内气流速度大,使未完全反应的固体颗粒被气体带出,降低碳的转化率,难以满足化工、冶金等领域对可燃气高热值的需求。气流床反应温度高,气化强度大,碳转化率高,然而原料灵活性较差,难以处理大颗粒原料,如生物质、石油焦和无烟煤等难以研磨的固体燃料,大大限制气流床的使用范围。上述气化技术各有优缺点,但从投资规模、大型化、原料灵活性综合来看,流化床气化技术具有较高的竞争力。但流化床由于其结构特点,会产生一定量含碳量的飞灰,常规处理方式是将其送往工业锅炉或电厂锅炉进行燃烧,充分利用其剩余热量,但由于飞灰挥发份极低,着火困难,且容易造成炉膛结焦等问题,因此一直是流化床技术推广过程中的难题。另外,常规飞灰处理方式锅炉需过氧燃烧,使反应温度提高,导致锅炉烟气中氮氧化物浓度增加,增重脱硝辅助系统的负荷,使运行成本提高。经检索,中国专利申请,公开号:cn103911179a,公开日:2014.07.09,公开了一种煤气化方法和装置。该煤气化方法包括:将粉煤和气化剂送入循环流化床气化炉进行反应;使反应生成的气化炉烟气经第一气固分离器分离出返料粉煤和带粉煤气流,并将返料粉煤循环回循环流化床气化炉继续反应,将带粉煤气流经第二气固分离器分离出煤气和含碳飞灰;将含碳飞灰送入热风炉,使其在高于1300℃燃烧,将产生的热风炉烟气返回循环流化床气化炉中参加反应,而燃烧产生的液态渣经冷却后排出。该发明提供的煤气化方法和装置克服了现有使用循环流化床进行煤气化的产品中飞灰量大、含碳量高的问题,降低了渣的含碳量,从而达到煤炭有效利用的目的。但该发明中循环流化床需要不断的补充气化剂而没有达到高温烟气循环利用的目的。技术实现要素:1.发明要解决的技术问题针对现有技术中存在气流床对燃料灵活性差、调节范围小,常规飞灰处理方式中利用率差、运行成本高的问题,本发明提供了一种气流床与循环流化床组合循环气化系统及其两段式气化方法。改变了传统处理循环流化床飞灰的方法,达到了将飞灰中的残炭合理利用、提高固体燃料利用率的目的。2.技术方案为达到上述目的,本发明提供的技术方案为:一种气流床与循环流化床组合循环气化系统,包括互相连通的气流床和循环流化床,气流床气化采用整个系统的飞灰作为原料,飞灰循环利用,提高了燃料的利用率,循环流化床气化采用气流床产的一定温度压力的烟气作为一次风和气化剂,烟气再利用使循环流化床无需持续的补充一次风和气化剂,通过调节气流床的压力、氧气与飞灰含碳的质量比,使循环流化床产生的可燃性气体产物压力、热值可调范围大,能够实现飞灰零排放,固体燃料综合利用率达到99%以上。进一步的技术方案,还包括和循环流化床依次通过气管连通的气固分离器、换热器ⅰ、除尘器和气站,达到净化可燃性气体的目的;气固分离器底部通过返料管道和循环流化床相通,大颗粒燃料循环在循环流化床内反应,直至全部反应完毕,以提高燃料的利用率,所述除尘器的底部飞灰通过飞灰输送管和气流床的顶部燃烧器相通,达到飞灰的循环利用,充分反应;所述气流床开有气化剂出口,通过管道和循环流化床相通,以提供循环流化床反应所需要的一次风和气化剂而无需额外提供,以达到二次利用。进一步的技术方案,所述除尘器的底部和气流床锁斗、给料罐依次通过飞灰输送管连通后,给料罐再通过飞灰输送管和气流床的顶部燃烧器相通,气流床锁斗起到飞灰的暂存作用,给料罐起到飞灰的贮存作用,并可以补充其它来源的飞灰,以提高气流床供料的稳定性。进一步的技术方案,所述气固分离器为旋风分离器,达到气固两相分离率高的目的;所述气流床内置换热器ⅱ,以调节气流床的出气温度;所述气流床和循环流化床的正下方配置渣池,方便回收利用;所述换热器ⅰ通过冷媒进口、冷媒出口和余热利用单元相通,避免热源的浪费;所述除尘器为布袋除尘器,除尘彻底。一种气流床与循环流化床组合循环气化系统的两段式气化方法,步骤为:步骤一、燃料反应:规定粒径的燃料由燃料仓输送到循环流化床,并利用气流床提供的气化剂,发生氧化还原反应;步骤二、分离:循环流化床内反应产生的含尘可燃性气体产物进入通过气管进入气固分离器分离;步骤三、循环流化:气固分离器分离后的大颗粒通过返料管道返回循环流化床循环反应;步骤四、可燃性气体产物除尘:气固分离器分离后的可燃性气体产物通入除尘器除尘,将可燃性气体产物中的飞灰分离,除尘后的可燃性气体产物通入气站;步骤五、飞灰气化燃烧:分离后的飞灰通过气力输灰单元和飞灰输送管输入气流床进行两段式气化燃烧;步骤六、烟气再利用:气流床产生的一定温度压力的烟气作为循环流化床的一次风和气化剂通过气化剂出口进入循环流化床;通过以上步骤达到飞灰的合理循环利用,理论上讲,飞灰可以持续循环利用,以提高燃料的利用率。进一步的两段式气化方法,步骤四中,气固分离器分离后的可燃性气体产物先通过换热器ⅰ冷却后再通入布袋除尘器除尘,两段式除尘,即达到清洁可燃性气体产物的目的,又提高了燃料利用率;换热器ⅰ外接余热利用单元,避免热量浪费。进一步的两段式气化方法,飞灰的热值不低于3500cal/kg,以达到即能提高燃料利用率又避免含热值过低时系统无法进行气化燃烧的目的;所述气流床为循环流化床提供750℃-1200℃的高温一次风和气化剂,以适应循环流化床下部密相区的反应温度。进一步的两段式气化方法,气流床的压力在0-5mpa范围内调节,氧气与飞灰含碳的质量比为1-4范围,通过调节气流床的压力、氧气与飞灰含碳的质量比,使循环流化床产生的可燃性气体产物压力、热值可调范围大,以适应不同的用户需求。进一步的两段式气化方法,气流床气化剂为纯氧、富氧空气、空气、水蒸气或二氧化碳中的一种或多种气化剂;所述气站续接脱硫单元后供用户使用。进一步的两段式气化方法,所述燃料为煤、生物质、城市垃圾、高含水固体废弃物、石油焦中一种或多种固体燃料;能够适用于能被循环流化床利用的所有固体燃料,粒径(小于10mm)要求范围宽,应用面广。3.有益效果采用本发明提供的技术方案,与现有技术相比,具有如下有益效果:(1)本发明的一种气流床与循环流化床组合循环气化系统,将气流床与循环流化床组合成一个循环气化系统,气流床气化采用循环流化床气化系统的飞灰作为原料,循环流化床气化采用气流床产的一定温度压力烟气作为一次风和气化剂,通过调节气流床的压力、氧气和固体燃料的质量比,使循环流化床产生的可燃性气体产物压力、热值可调范围大,飞灰在闭环内循环,实现了飞灰的零排放,燃料的综合利用率能达到99%以上;(2)本发明的一种气流床与循环流化床组合循环气化系统,改变传统处理循环流化床飞灰的方法,将飞灰中的残炭合理利用,大大提高固体燃料的利用率;该方法可燃性气体产物热值可调性强,能够满足化工、冶金、陶瓷等不同行业对不同热值可燃性气体产物的需求;(3)本发明的一种气流床与循环流化床组合循环气化系统,气固分离器分离大颗粒燃料返回循环流化床进行二次循环反应,直至其形成飞灰;除尘器分离出飞灰和洁净可燃性气体产物,飞灰输送至气流床作为气流床原料进行二次循环反应,直至其反应完全,实现能量的多级利用,提高燃料利用效率,降低三废排放,节能、清洁环保;而且,循环流化床反应所需要的气化剂而无需额外提供,并能够循环利用;(4)本发明的一种气流床与循环流化床组合循环气化系统,气流床锁斗和给料罐对飞灰起到暂存和补充的作用,提高了气流床供料的稳定性;(5)本发明的气流床与循环流化床组合循环气化系统,旋风分离器固气分离效率高,配合布袋除尘器的除尘,一个分离可燃性气体产物内大颗粒,避免大颗粒燃料进入气流床,一个分离小颗粒飞灰,洁净可燃性气体产物,起到协同作用的效果;而且,换热器ⅰ将过热可燃性气体产物降温,避免过热颗粒将布袋除尘器损坏,和布袋除尘器也达到了协同作用的效果;(6)本发明的一种气流床与循环流化床组合循环气化系统的两段式气化方法,达到了飞灰的循环利用,理论上讲,飞灰可以持续循环反应利用,以提高燃料的利用率;(7)本发明的气流床与循环流化床组合循环气化系统的两段式气化方法,两段式除尘,即达到清洁可燃性气体产物的目的,又提高了燃料利用率;换热器ⅰ外接余热利用单元,避免热量浪费;(8)本发明的两段式气化方法,飞灰热值不低于3500cal/kg,以达到既能提高燃料利用率又避免热值过低时系统无法气化燃烧的目的;(9)本发明的一种两段式气化方法,能够使产生的可燃可燃性气体产物热值在1200kcal/nm3-3500kcal/nm3范围内可调,压力在0-5mpa范围内可调,以适应不同的用户需求;(10)本发明的一种两段式气化方法,能够适用于能被循环流化床利用的所有固体燃料,粒径(小于10mm)要求范围宽,应用面广;(11)本发明的气流床与循环流化床组合循环气化系统,气流床和循环流化床共用一套换热、除尘、脱硫系统,减少了投资成本。附图说明图1为本发明的气流床与循环流化床组合循环气化系统结构示意图;图2为本发明的工艺流程图。图中:1、气流床;2、循环流化床;3、气固分离器;4、换热器ⅰ;5、除尘器;6、气流床锁斗;7、给料罐;8、渣池;9、气管;10、飞灰输送管;11、气化剂出口;12、换热器ⅱ;41、冷媒进口;42、冷媒出口;100、燃料仓;200、气站。具体实施方式为进一步了解本发明的内容,结合附图对本发明作详细描述(注:如未特别注明,实施例中含量表示为重量含量)。实施例1本实施例的气流床与循环流化床组合循环气化系统,其生产工艺流程如图1所示,包括煤粉破碎及输运单元、原煤仓、循环流化床、气流床、渣池、换热除尘系统和气力输灰单元,其中,循环流化床、气流床和换热除尘系统形成一个闭路的循环,气流床气化采用整个系统的飞灰作为原料,飞灰循环利用,提高了燃料的利用率,循环流化床气化采用气流床产的一定温度和压力的烟气作为一次风和气化剂,烟气能够再利用,循环流化床无需持续的补充一次风和气化剂;换热除尘系统可以先连接飞灰贮存罐后再和气流床相通,以达到供料稳定的目的,换热除尘系统还可以外接余热利用单元,避免热量浪费,换热除尘系统的煤气出口和脱硫系统连接后再和工业用户连接,避免煤气燃烧产物造成环境污染。实施例1中采用的固体燃料为烟煤,煤质分析如下表1:表1实施例1中采用的固体燃料为烟煤的煤质分析全水%空干基水分%空干基灰分%空干基固定碳%空干基挥发分%空干基全硫%11.078.2115.8948.5127.390.33主要生产工艺为:原煤经破碎筛分,合格粒径的粉煤输送到原煤仓后,输送至循环流化床,粉煤在循环流化床内发生氧化还原反应,产生的含尘煤气进入换热除尘系统分离,换热除尘系统可以是旋风分离器和除尘单元的组合,分离后的大颗粒被旋风分离器分离返回循环流化床,经分离后的煤气进入余热利用单元,降温后的煤气进入除尘单元,将煤气中的飞灰分离,飞灰通过气力输灰单元送往气流床气化燃烧;气流床产生带有一定压力的高温气体作为循环流化床的气化剂,渣排入渣池,送往循环流化床气化。经除尘单元除尘后的煤气送往脱硫系统脱除h2s,得到清洁煤气送往用户。气流床与循环流化床组合循环气化系统可以通过调节压力和氧气和固体燃料的质量比,来满足用户热值需求,净化后煤气经脱硫单元,脱除煤气中的h2s,使其含量低于20mg/nm3后送到至用户,副产硫磺外卖。单元副产的中低压饱和蒸汽和过热蒸汽,除工艺需求或单元伴热外,外送其他需求用户。通过本实施例的气流床与循环流化床组合循环气化系统,煤炭利用率高于99%,煤气含尘≤10mg/nm3,h2s含量≤20mg/nm3,无氮氧化物等污染物排放,节能减排。实施例2本实施例的气流床与循环流化床组合循环气化系统,基本结构同实施例1,不同和改进之处在于,如图2所示,包括互相连通的气流床1、循环流化床2,还包括和循环流化床2依次通过气管9连通的气固分离器3、换热器ⅰ4、除尘器5和气站200,气流床1气化采用整个系统的飞灰作为原料,飞灰循环利用,提高了燃料的利用率,循环流化床2气化采用气流床1产的一定温度压力的烟气作为一次风和气化剂,烟气也能够循环利用,循环流化床2无需持续的补充气化剂,通过调节气流床1的压力、氧气和固体燃料的质量比,使循环流化床2产生的煤气压力、热值可调范围大,能够实现飞灰零排放。气固分离器3底部通过返料管道和循环流化床2相通,大颗粒燃料循环在循环流化床2内反应,直至全部反应完毕,以提高燃料的利用率,并提高了燃料的投放粒径,提高燃料进入循环流化床2的粒径范围;所述除尘器5的底部飞灰通过飞灰输送管10和气流床1的顶部燃烧器相通,达到飞灰的循环利用,充分反应;所述气流床1开有气化剂出口11,通过管道和循环流化床2相通,以提供循环流化床2反应所需要的气化剂而无需额外提供。本实施例的气流床与循环流化床组合循环气化系统的两段式气化方法,步骤为:步骤一、燃料反应:将燃料颗粒,比如煤、生物质、城市垃圾、高含水固体废弃物、石油焦中一种或多种固体燃料的混合物,由燃料仓100输送到循环流化床2,并利用气流床1提供的气化剂,发生氧化还原反应;步骤二、分离:循环流化床2内反应产生的含尘煤气进入通过气管9进入气固分离器3分离;步骤三、循环流化:气固分离器3分离后的大颗粒通过返料管道返回循环流化床2循环反应;步骤四、煤气除尘:气固分离器3分离后的煤气通入除尘器5除尘,将煤气中的飞灰分离,除尘后的煤气通入气站200;步骤五、飞灰气化燃烧:分离后的飞灰通过气力输灰单元和飞灰输送管10输入气流床1进行两段式气化燃烧;步骤六、烟气再利用:气流床1产生的一定温度压力的烟气作为循环流化床2的一次风和气化剂通过气化剂出口11进入循环流化床2。通过以上步骤达到飞灰的循环利用,理论上讲,飞灰可以持续循环利用,以提高燃料的利用率。实施例3本实施例的气流床与循环流化床组合循环气化系统,基本结构同实施例2,不同和改进之处在于,所述除尘器5的底部和气流床锁斗6、给料罐7依次通过飞灰输送管10连通后,给料罐7再通过飞灰输送管10和气流床1的顶部燃烧器相通,气流床锁斗6起到飞灰的暂存作用,给料罐7起到飞灰的贮存作用,并可以补充其它来源的飞灰,以提高气流床1供料的稳定性。本实施例的气流床与循环流化床组合循环气化系统的两段式气化方法,步骤为:步骤一、燃料反应:将煤粉破碎至小于15mm后,转入燃料仓100暂存,再由燃料仓100输送到循环流化床2,并利用气流床1提供的气化剂,发生氧化还原反应;步骤二、分离:循环流化床2内反应产生的含尘煤气进入通过气管9进入气固分离器3分离;步骤三、循环流化:气固分离器3分离后的大颗粒通过返料管道返回循环流化床2循环反应;步骤四、煤气除尘:气固分离器3分离后的煤气通入除尘器5除尘,将煤气中的飞灰分离,除尘后的煤气通入气站200;步骤五、飞灰气化:分离后的飞灰通过气力输灰单元和飞灰输送管10先输入气流床锁斗6暂存后,落入给料罐7贮存,再通过气力输送将飞灰送入气流床1进行两段式气化燃烧;步骤六、烟气再利用:气流床1产生的高温高压气体作为循环流化床2的气化剂通过气化剂出口11进入循环流化床2。实施例4本实施例的气流床与循环流化床组合循环气化系统,基本结构同实施例3,不同和改进之处在于,气固分离器3为旋风分离器,达到气固两相分离率高的目的;所述气流床1内置换热器ⅱ12,以调节气流床1的出气温度;所述气流床1和循环流化床2的正下方配置渣池8,方便回收循环利用;所述换热器ⅰ4通过冷媒进口41、冷媒出口42和余热利用单元相通,冷媒可以用冷空气或冷却水,避免热源的浪费;所述除尘器5为布袋除尘器,除尘彻底。本实施例的气流床与循环流化床组合循环气化系统的两段式气化方法,步骤为:步骤一、燃料反应:将煤粉破碎至小于10mm后,转入燃料仓100暂存,再由燃料仓100输送到循环流化床2,并利用气流床1提供的高温烟气作为一次风和气化剂,发生氧化还原反应;步骤二、分离:循环流化床2内反应产生的含尘煤气进入通过气管9进入旋风分离器分离;步骤三、循环流化:旋风分离器分离后的大颗粒通过返料管道返回循环流化床2循环反应;步骤四、煤气除尘:旋风分离器分离后的煤气通入换热器ⅰ4冷却后再通入布袋除尘器除尘,避免过热颗粒将布袋除尘器损坏,和布袋除尘器也达到了协同作用的效果,布袋除尘器将煤气中的飞灰分离,除尘后的煤气通入气站200;换热器ⅰ4可以外接余热利用单元,避免热量浪费;步骤五、飞灰气化:分离后的飞灰通过气力输灰单元和飞灰输送管10先输入气流床锁斗6暂存后,落入给料罐7贮存,再通过气力输送将飞灰送入气流床1进行两段式气化燃烧;步骤六、烟气再利用:气流床1产生的高温高压气体作为循环流化床2的一次风和气化剂通过气化剂出口11进入循环流化床2。实施例5本实施例的气流床与循环流化床组合循环气化系统的两段式气化方法,基本步骤同实施例4,不同和改进之处在于,气流床1的压力在0-5mpa范围内调节,氧气和飞灰含碳的质量比为1-4范围调节,使热值在1200-3500kcal/nm3范围内可调大,在本实施例中,通过调节气流床1的压力分别为0.05mpa、2.07mpa,氧气和飞灰含碳的质量比2,使循环流化床2产生的煤气压力分别为0.01mpa、2.0mpa,使产生的煤气热值分别为1496kcal/nm3、2643kcal/nm3,以适应不同的用户需求。实施例6本实施例的气流床与循环流化床组合循环气化系统的两段式气化方法,基本步骤同实施例5,不同和改进之处在于,所述气流床1为循环流化床2提供750℃-1200℃的高温气化剂,以适应循环流化床2下部密相区的反应温度,可以通过换热器ⅱ12调节气化剂温度,也可以通过气流床1采用不同压力的高富氧或纯氧气化工艺,来达到750℃以上的高温气化剂。实施例7本实施例的气流床与循环流化床组合循环气化系统的两段式气化方法,基本步骤同实施例6,不同之处在于:可以通过检测飞灰含碳量来判定飞灰是否需要循环利用,飞灰热值不低于3500kcal/kg,以达到即能提高燃料利用率又避免含碳量过低时系统气化效率降低的目的。实施例8本实施例的气流床与循环流化床组合循环气化系统的两段式气化方法,基本步骤同实施例7,不同之处在于:气流床1气化剂为纯氧、富氧空气、空气、水蒸气或二氧化碳中的一种或多种气化剂,本实施例中以纯氧、30%富氧空气、空气为气化剂,根据煤气压力和热值需要进行相应的选择,如表2所示;所述气站200续接脱硫单元后供用户使用。表2实施例8中不同气流床气化剂对应的气流床压力和热值气流床气化剂气流床压力mpa热值kcal/nm3空气0.05149630%富氧空气0.051721纯氧0.052729实施例9本实施例的气流床与循环流化床组合循环气化系统的两段式气化方法,基本步骤同实施例7,不同之处在于:应用于生物质、城市垃圾、高含水固体废弃物、石油焦中一种或多种固体燃料的气化。以上示意性的对本发明及其实施方式进行了描述,该描述没有限制性,附图中所示的也只是本发明的实施方式之一,实际的结构并不局限于此。所以,如果本领域的普通技术人员受其启示,在不脱离本发明创造宗旨的情况下,不经创造性的设计出与该技术方案相似的结构方式及实施例,均应属于本发明的保护范围。当前第1页12