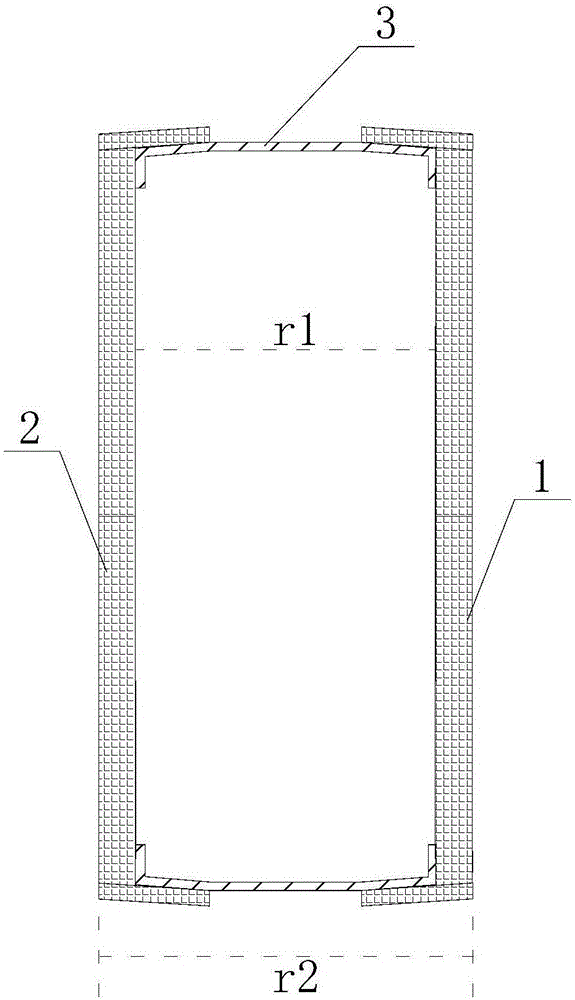
本发明涉及风电叶片制造
技术领域:
,特别涉及一种风电叶片腹板吊装方法。
背景技术:
:风电叶片作为机组的核心部件,风电叶片技术是风力发电系统的核心技术之一,其主要由叶片的吸力面(SS)壳体、压力面(PS)壳体与腹板通过粘接剂粘接而成,腹板包括前缘腹板和与其对称设置的后缘腹板。腹板吊装是腹板结构与壳体粘接的第一步,吊装的方法决定了腹板的质量及后续叶片的生产效率。传统腹板吊装方法是使用绑带将腹板由SS粘接面托起后与行车固定进行运输,吊装至合适位置后将绑带抽出。此方法浪费时间,劳动强度大。并且影响腹板粘接和定位效果。技术实现要素:本发明提出一种风电叶片腹板吊装方法,解决了现有技术中效率低、劳动强度大,而且影响腹板粘接和定位效果的问题。本发明的一种风电叶片腹板吊装方法,包括:S1:腹板脱模修型后,从腹板在模具中的定位长度4m处开始,向长度方向间隔预定距离固定一块U型块,以保证在腹板长度方向上的预定区域的前缘腹板和后缘腹板的内侧间隙的宽度达到预定宽度,所述预定距离为1.8~2.2米;S2:起吊腹板前,根据腹板对应叶根、叶身和叶尖三个区域的前缘腹板和后缘腹板内侧间隙的宽度,选择与内层宽度尺寸配套的起吊工装;S3:在腹板对应的叶根区域,将起吊工装的内侧工装旋转至与腹板轴向平行,外侧工装与腹板轴向垂直,将内侧工装通过腹板内侧间隙放入,旋转内侧工装使其与腹板轴向垂直,外侧工装卡住前缘腹板和后缘腹板各自的外侧;S4:在腹板对应的叶身、叶尖区域重复S3步骤,以安装叶身、叶尖区域的起吊工装;S5:将三个起吊工装与行车固定后,用行车将腹板吊装至叶片的吸力面壳体及压力面壳体分别与腹板粘接的粘接区域;S6:将腹板放置在壳体上后,取下起吊工装。其中,所述步骤S1中采用手糊玻纤布的方式固定所述U型块。其中,所述步骤S1中,所述预定距离为2米。其中,距腹板在模具中的定位端开始,离定位端距离不同的粘接区域与U型块长度的对应关系为:4.5m-14m距离的粘接区域对应的U型块长度为180mm,16m-22m距离的粘接区域对应的U型块距离为170mm,24m-30m距离的粘接区域对应的U型块长度为180mm,32m-38m距离的粘接区域对应的U型块长度为190mm,40m-48m距离的粘接区域对应的U型块长度为180mm。本发明的方法中采用腹板起吊工装将腹板吊装至粘接区域,而且采用U型块保证在吊装过程中前后腹板间的间距,极大的降低了腹板吊装的时间,提高生产效率,不会对腹板粘接面造成破坏,不会影响粘接效果,去掉工装的过程也不会影响腹板原有的定位,极大的提高产品的质量及安全性。附图说明为了更清楚地说明本发明实施例或现有技术中的技术方案,下面将对实施例或现有技术描述中所需要使用的附图作简单地介绍,显而易见地,下面描述中的附图仅仅是本发明的一些实施例,对于本领域普通技术人员来讲,在不付出创造性劳动性的前提下,还可以根据这些附图获得其他的附图。图1为本发明的风电叶片腹板吊装方法中腹板沿长度方向上制作U型块的间隔距离示意图;图2为本发明的风电叶片腹板吊装方法中在前后缘腹板之间制作完U型块后的截面示意图;图3为本发明的风电叶片腹板吊装方法采用的起吊工装示意图;图4为本发明的风电叶片腹板吊装方法中采用工装吊装腹板的结构示意图;图5为腹板与叶片壳体粘接后的示意图。具体实施方式下面将结合本发明实施例中的附图,对本发明实施例中的技术方案进行清楚、完整地描述,显然,所描述的实施例仅仅是本发明一部分实施例,而不是全部的实施例。基于本发明中的实施例,本领域普通技术人员在没有作出创造性劳动前提下所获得的所有其他实施例,都属于本发明保护的范围。本实施例的一种风电叶片腹板吊装方法,包括:步骤S1,如图1所示,腹板脱模修型后,从腹板在模具中的定位长度4m处开始,向长度方向间隔预定距离固定一块U型块,以保证在腹板长度方向上的预定区域(即在粘接时的粘接区域)的前缘腹板和后缘腹板的内侧间隙的宽度达到预定宽度,所述预定距离为1.8~2.2米。固定完U型块后的截面图如图2所示,前缘腹板1和后缘腹板2内侧的间隙固定U型块3,截面的上下两端各固定一块U型块3,以保证前缘腹板1和后缘腹板2内侧间隙达到预定宽度。步骤S2,起吊腹板前,根据腹板对应叶根、叶身和叶尖三个区域的前缘腹板和后缘腹板内侧间隙的宽度,选择与内层宽度尺寸配套的起吊工装。如图3所示,起吊工装包括:立柱4,外侧工装5和内侧工装6,外侧工装5和内侧工装6形状相同,内侧工装6的尺寸小于外侧工装5,内侧工装5可绕立柱4的轴线转动地安装在立柱4的一端,外侧工装5固定在内侧工装6上方。由于叶片在长度方向上尺寸不同,因此需要的起吊工装尺寸也不同。步骤S3,如图4所示,在腹板对应的叶根区域,将起吊工装的内侧工装6旋转至与腹板轴向平行,外侧工装5与腹板轴向垂直,将内侧工装通过腹板内侧间隙放入,旋转内侧工装6使其与腹板轴向垂直,外侧工装5卡住前缘腹板1和后缘腹板2各自的外侧,即外侧工装5两端的间距稍大于外侧间距r2,内侧工装6两端的间距稍小于内侧间距r1。步骤S4,在腹板对应的叶身、叶尖区域重复S3步骤,以安装叶身、叶尖区域的起吊工装;步骤S5,将三个起吊工装与行车固定后,用行车将腹板吊装至叶片的吸力面壳体及压力面壳体分别与腹板粘接的粘接区域;步骤S6,如图5所示,将腹板放置在壳体上后,取下起吊工装。具体地,分别将叶根、叶身和叶尖处内侧工装旋转至与腹板轴向平行,将腹板吊装工装从腹板内侧间隙处取出,放置在工装存放处待下次使用。其中,叶片截面圆弧的一端为前缘,尖头的一端为后缘,叶片上与腹板粘接的区域形成有PS梁帽7和SS梁帽8。本实施例的方法中采用腹板起吊工装将腹板吊装至粘接区域,而且采用U型块保证在吊装过程中前后腹板间的间距,极大的降低了腹板吊装的时间,提高生产效率,不会对腹板粘接面造成破坏,不会影响粘接效果,去掉工装的过程也不会影响腹板原有的定位,极大的提高产品的质量及安全性。本实施例中,步骤S1中采用手糊玻纤布的方式固定U型块3,玻纤布质量轻,而且手糊方式是在固定好前缘腹板1和后缘腹板2后进行,能够保持前缘腹板1和后缘腹板2的间距不会因为固定U型块3而发生微小变化。步骤S1中,预定距离为2米,以方便测量。本实施例中,距腹板在模具中的定位端开始,离定位端不同距离的粘接区域与U型块长度的对应关系为:4.5m-14m距离的粘接区域对应的U型块长度为180mm,16m-22m距离的粘接区域对应的U型块距离为170mm,24m-30m距离的粘接区域对应的U型块长度为180mm,32m-38m距离的粘接区域对应的U型块长度为190mm,40m-48m距离的粘接区域对应的U型块长度为180mm。具体见下表:粘接区域离定位端距离4.5m-14m16m-22m24m-30m32m-38m40m-48mU型块长度180mm170mm180mm190mm180mm由于叶片的形状在其长度方向上的变化,因此U型块的长度(即前后缘腹板的内侧间隙的距离)也不同,上述粘接区域离定位端距离与U型块长度的对应关系更加适合叶片的形状,使得腹板和叶片壳体粘接更牢固。以上所述仅为本发明的较佳实施例,并不用以限制本发明,凡在本发明的精神和原则之内,所作的任何修改、等同替换、改进等,均应包含在本发明的保护范围之内。当前第1页1 2 3